How Wafer Handling Automation Improves Process Control
- kensingtonlabsus
- Mar 18, 2020
- 2 min read
The wafer handling automation has become a powerful & convenient approach to protect the silicon wafers from the dust elements or small microns that plays a vital role in blocking the structure and halts up the overall performance of electronic devices. Due to the advancements in tools and technologies, it becomes possible for the semi-conductor companies to introduce the fully automated wafer handler for improving the front-end & back-end processes.
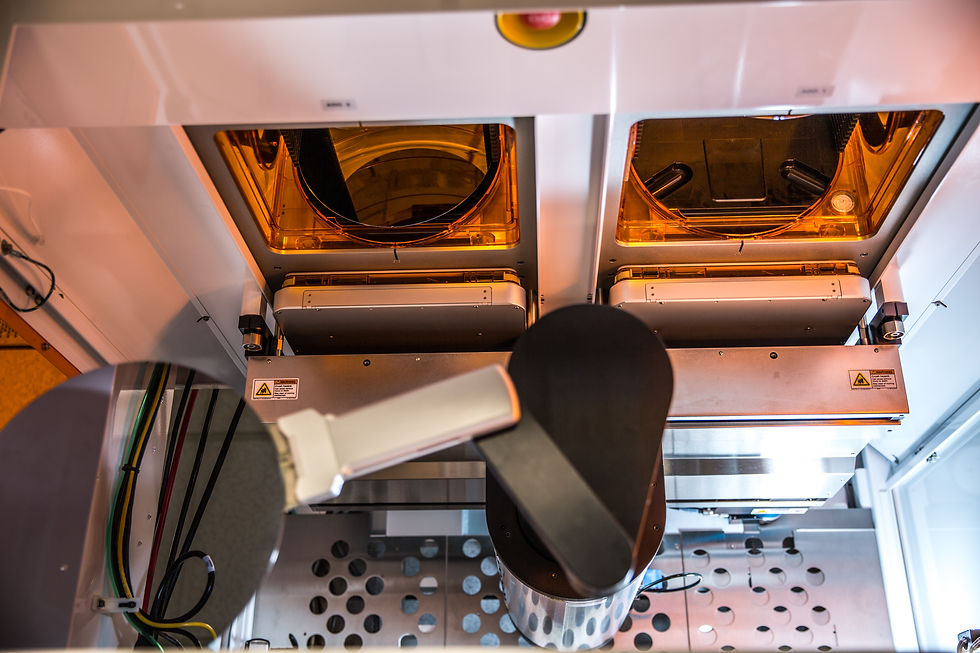
The key benefits of using wafer automation are as follows:
Reliable Chemical Distribution
In fully wafer automation, semi-conductor OEMs (Original Equipment Manufacturer) uses the several subsystems & co-developing components to disperse the right amount of chemicals and gases in microchips. Purity is the fundamental concern for the semiconductors that can be reused & recovered in the future. But some industries still use non-filtered water and gaseous elements that increase the risk of pollutants & even creates waste disposal problems. Therefore, it is essential to get the assistance of automated wafers to minimize the waste in industries.
No meters required
The wafer handling equipment doesn’t require any meters or weight machines to calculate the chemical ratio. As it works on the software that automatically detects how much gases or chemicals are needed in one chip or to perform the particular process. Due to this methodology, workers can save their efforts in terms of adding or removing the chemicals again & again. The automatic operations guarantees that workers will stay safe from toxic substances and can manage the processes hassle-free.
High-quality
The low energy consumption, 360-degree rotation, ergonomic design, easy loading & filling, customized controls make the wafer handling end effector ready to use & capable of delivering high-quality. Apart from this, the data logging is possible with the wafer handling automation, but it will require an Ethernet connection to track the processed variables.
Repeatability
The automated edge-grip system offers around 300mm of safe wafer handling in which robots are performed with the optical-sensing device to measure the environment and functionality. Similarly, with sensors, it can easy to detect whether the wafers are on the accurate position and where it needs to be placed. In case of inaccurate positioning, the system will lift it & pushed backward until the properly operated actuator is mounted at the end of the gripper.
Budget-friendly option
The implementation of mechanized wafer fabrication costs less in comparison to the manually operated equipment for semiconductors. The main reasons are the real-time controls and the minimal chemical usage that makes it easier to boost the production line performance.
The Final Thought
If you are looking for the high-rigidity linear subsystems, well-balanced servo drives, no backlash, or overshoot problems in machines, you should consider the wafer handling automation to experience the smoother operations in the real-time. You can also discover the Kensington Labs that offers the tailored-made motion controls, load ports, robotics, and precision stages in the most affordable range.
Comments